Employee qualification in industrial battery production: an onboarding project
Simplified: Good structures and qualified employees make it work – which is already taken care of during recruiting and onboarding. So should you just hire electrical specialists? No, because would you tell your recruiting department, “please hire 200 electrical engineers for the battery factory, 30 of them master craftsmen and 40 engineers, and please do it in the course of three quarters of a year“Depending on their sense of humor, you will experience at least a chuckle or open rejection – because the job market doesn’t offer that now or in the foreseeable future, not a chance! Apart from this, the selection of specialists in industrial battery production is not necessarily a must or even expedient, even if the idea is obvious in the case of batteries, as they require electrical specialists throughout. However, they have a variety of requirements that also rely on experience in production, possibly even shift work; possibly more than the title of the vocational qualification. Your employees must work with the optimal structure that you provide, this is a very important factor in recruiting. Nevertheless, the importance of electrical engineering qualifications should not be underestimated, especially in battery production. The good news is: Yes, you can also qualify and deploy non-specialist employees without electrical engineering knowledge for battery work in production and development! However, you won’t be able to do it completely without electrical engineers.
The approach to qualification in a battery factory is also fundamentally different from the qualification requirements of small teams. The difference:
Small teams are often already established. The aim here is to consider which team members need which qualifications to be able to carry out which (new) activities and what limits are set for whom. Although the qualification is focused on the job requirements, it is completely person-oriented.
When it comes to setting up the complete production of batteries, individual lines, halls, shifts or complete factories, the question ideally arises during the recruitment process and is focused on demand from the outset. They define which activities must be carried out by how many people at which locations at what times and to what extent. On this basis, the qualification requirements of the expected candidates are estimated and then specified in the recruiting process and, if possible, even integrated into the onboarding process.
We are therefore happy to support you as a partner right from the planning stage and provide advice for the specialist department, HR and recruiting.
As with most planning topics, the same applies to employee qualification for battery production: the earlier this is taken into account in planning, the better processes can be created, the smoother and faster the point of production can be reached and the lower (because optimized) the overall qualification effort and thus a lot of different costs.
Our services include support in planning by designing legally compliant requirements for work in the production of batteries (i.e. electrical systems) as well as conducting training courses and certifying employees.
We would like to get to know you. Write to us at keyaccount@tcs-engineering.de, let’s talk first without obligation and then we can work together to get your battery production up and running faster, more effectively and safely.
The special features of employee training in battery production at an industrial level
Are your people in battery production only employed, or can and are they also allowed to work?
Safety training is an essential part of operational safety management. It serves to inform employees about risks, protective measures and rules of conduct in the workplace. However, the complexity and scope of these instructions can vary greatly depending on whether they are aimed at a single team or the entire staff of a battery factory.
Safety briefing for an individual team
When providing safety training to an individual team in a battery factory, the focus is on specific tasks and processes that the team performs. The instruction is usually more detailed and technical in nature, as it is tailored to the direct activities of the team members. It deals with specific risks associated with certain machines, chemicals or work processes and the corresponding protective measures.
Individual teams must be informed of the immediate emergency plans that apply to their specific working environment. This includes instructions for dealing with machine failures, battery fluid leaks or other specific hazardous situations. Responsibility for safety lies with both the team leaders and each individual team member. Everyone must know the safety protocols and be able to act accordingly.
Safety training for all staff
In contrast, the safety training for all personnel in a battery factory must be broader in scope. It must cover a variety of topics that are relevant to all employees, regardless of their specific role or position. This includes general safety rules, emergency procedures, evacuation plans and the use of personal protective equipment.
The challenge is to make the information understandable and accessible so that it can be understood by employees with different levels of technical understanding and from different areas of work. The training must overcome cultural and language barriers and ensure that every employee can absorb and implement the information.
Responsibility for security at this level lies with senior managers and security personnel. They must ensure that the safety culture is embedded throughout the company and that all employees are regularly trained and informed about changes in safety procedures.
Structural requirements for security
The structural security requirements also differ. When instructing a team, managers can focus on providing specific safety protocols and equipment required for the tasks at hand. However, when instructing all staff, broader safety measures must be taken into account, such as the safety of the building infrastructure, air quality and emergency exits.
Conclusion
In summary, the safety training of an individual team in a battery factory focuses on the specific needs and risks of that team, while the training of all personnel aims to create a broad understanding of safety practices and procedures. Both levels of safety training are critical to ensuring a safe working environment and must be carefully planned and implemented to address the structural requirements of safety and the responsibilities of each individual.
If you want to know more about battery technology and the structure of the corresponding qualification structure and would like to see an example of this, watch our 9:40 minute video (click). In it you will briefly learn the most important things to know as a responsible person, to be able to have a say and to take advantage of the opportunities that open up to you. We are also happy to answer any questions you may have, so please visit our page on battery technology qualification, whether for (ev) high voltage or plant engineering (click).
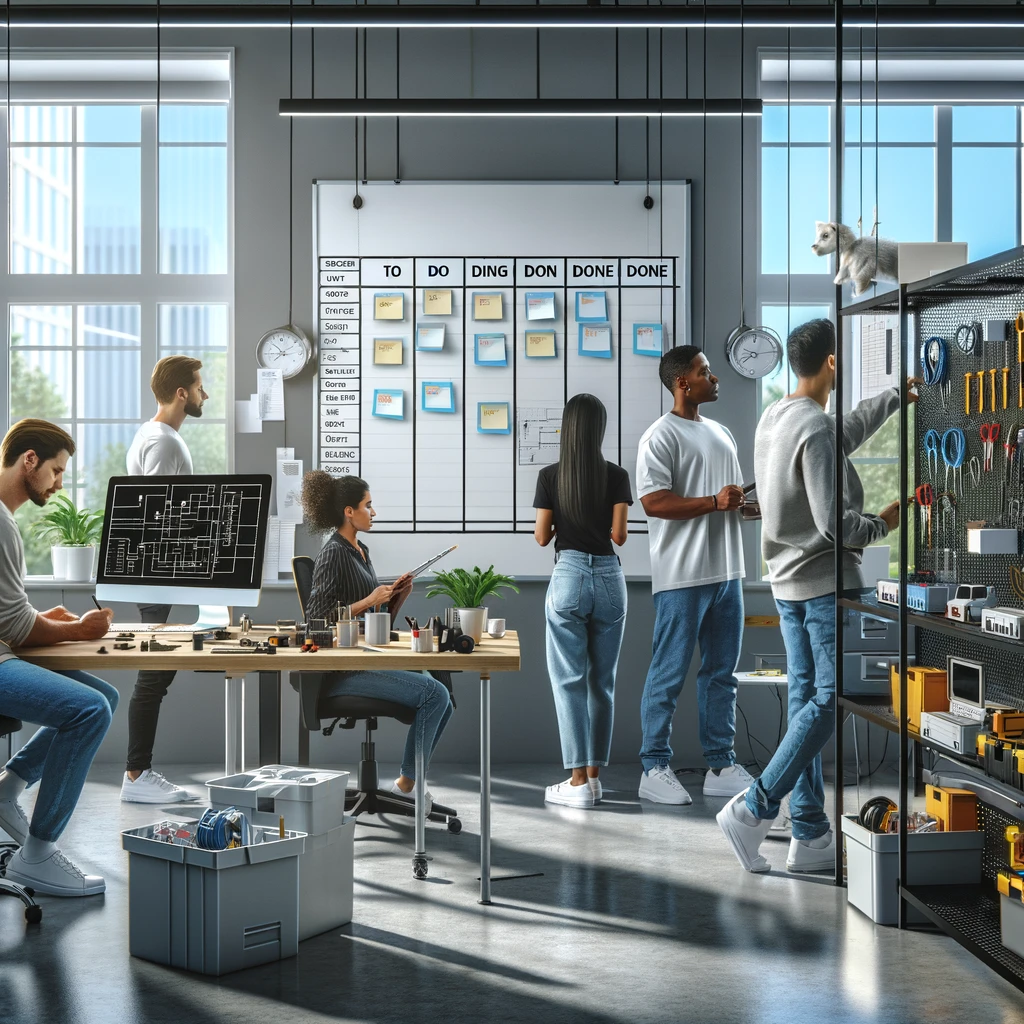
Leave A Comment